The method of corner welding affects both the aesthetic value of the window and the functionality of the construction. The traditional method of connecting profiles is associated with, among others, the need to remove the welding curb. The latest V-Perfect technology enables to obtain a smoothly finished welding spot that retains its impeccable appearance for years.
The traditional way of welding PVC profiles
The disadvantage of the traditional method of joining the corners is the need to remove the welding curb, i.e. the excess material flowing out during the profile welding process. There is no veneer in the place where the welded elements are joined – after getting rid of the excess material. Accordingly, a profile is visible in the welding area. To get rid of this cosmetic defect, special markers of a colour similar to the colour of the veneer are used. Unfortunately, they are not a perfect solution and start to wear off after some time. Additionally, this method of joining profiles makes the corners get dirty faster. This is due to the need to remove the welding curb by milling. This activity results in the appearance of pores, invisible to the naked eye, into which impurities enter. Compared to the traditional method of joining PVC profiles, the use of Graf Synergy SL4-FF EVO robots is a much better option, allowing for seamless corner welding.
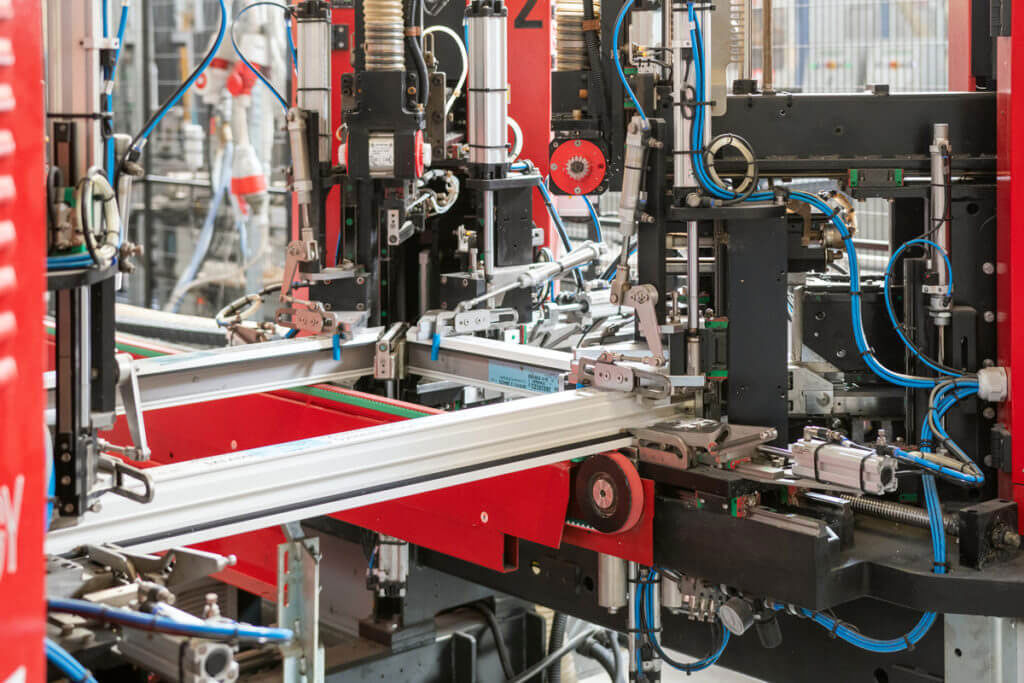

The welding effect is shown in the photos below.
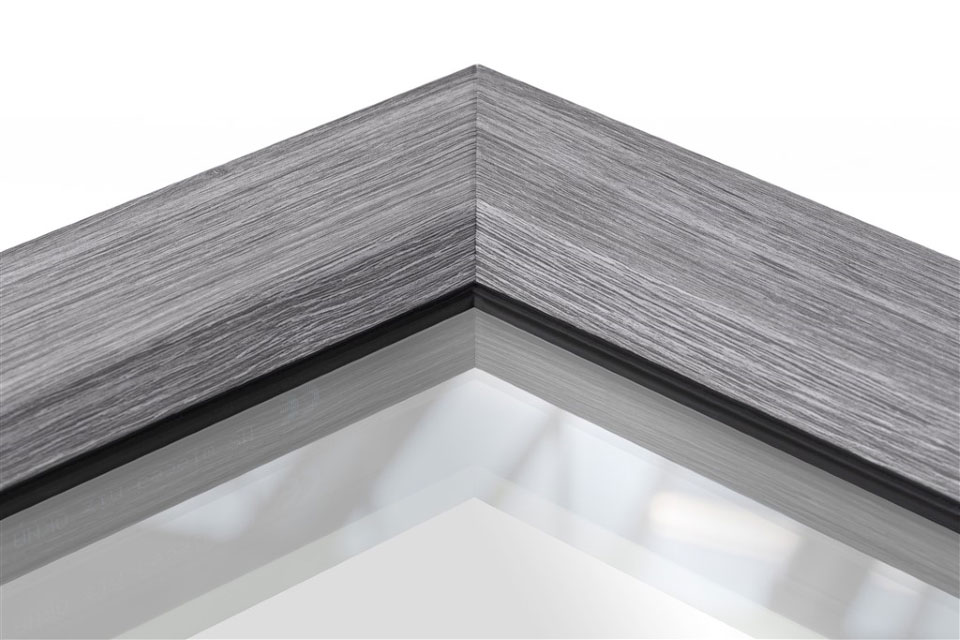
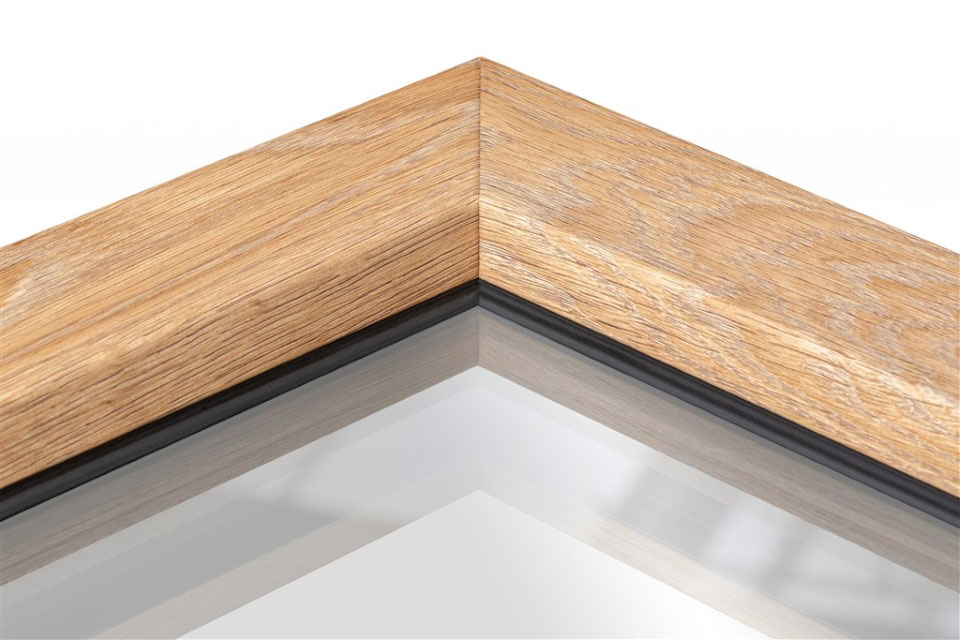
Seamless welding – advantages
Profiles welding with the use of Graf Synergy SL4-FF EVO robots enables a delicate V-Perfect groove to be obtained. The use of this seamless method prevents excess material from flowing out of the welding area. The foil is crimped at the point where two elements are joined. This allows to mask minor unevenness of the profiles and ensure appropriate aesthetics also with thin, delicate veneers. The use of this method also makes it possible to partially mask the effect of foil shining in the area of the weld. Using seamless welding makes the corner of the frame or sash smoothly finished. Undoubtedly, this has a positive effect on the aesthetic value of the window. It is also worth mentioning that the V-Perfect technology has a positive effect on the tightness of the structure. Due to numerous advantages, the Graf Synergy SL4-FF EVO robots are used in the production of windows available in the MS beyond WINDOWS offer.
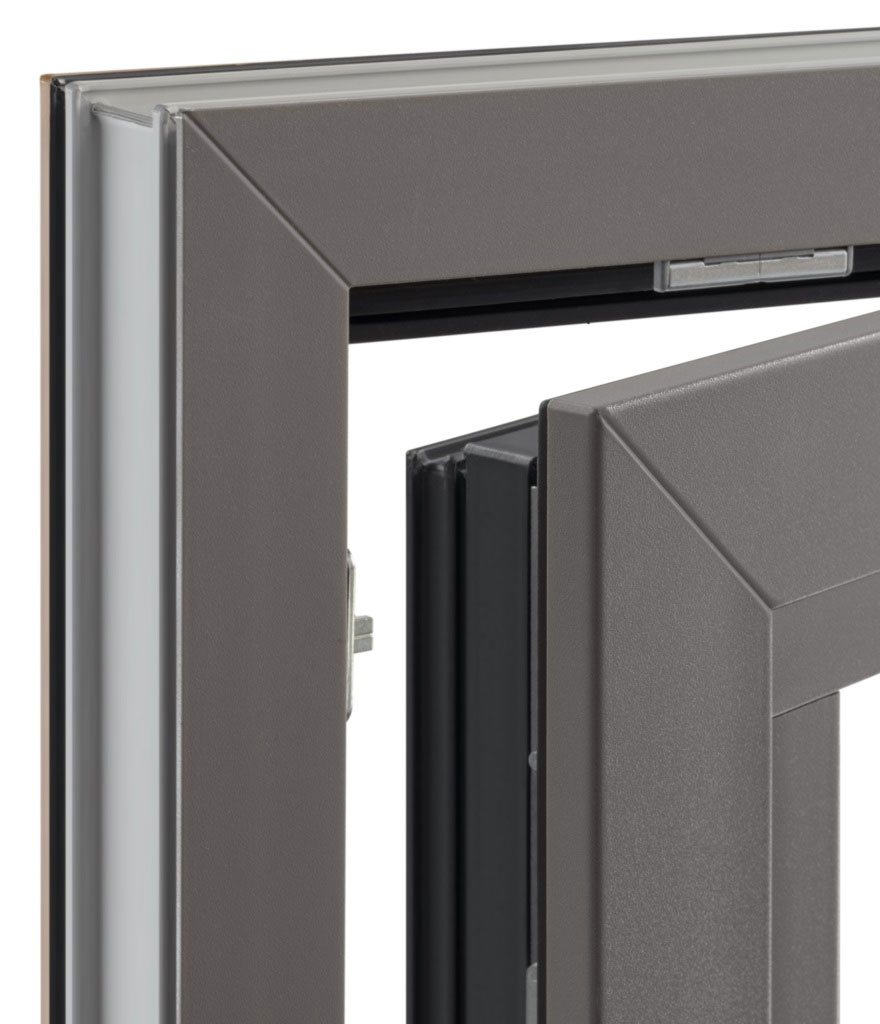
V-Perfect technology in MS beyond WINDOWS
Seamless welding is one of the newest technological solutions used in the MS beyond WINDOWS factory. Graf Synergy SL4-FF EVO robots are used to connect the corners of frames and sashes. The four-head welding machine enables seamless joining of frames and sashes. This process does not require the use of an additional device – a cleaning machine. Due to the fact that there is no need to perform additional mechanical processing, the result of the robot’s work is a finished window element. In addition, traditional “V” blasting welding is also used (it applies to white profiles).
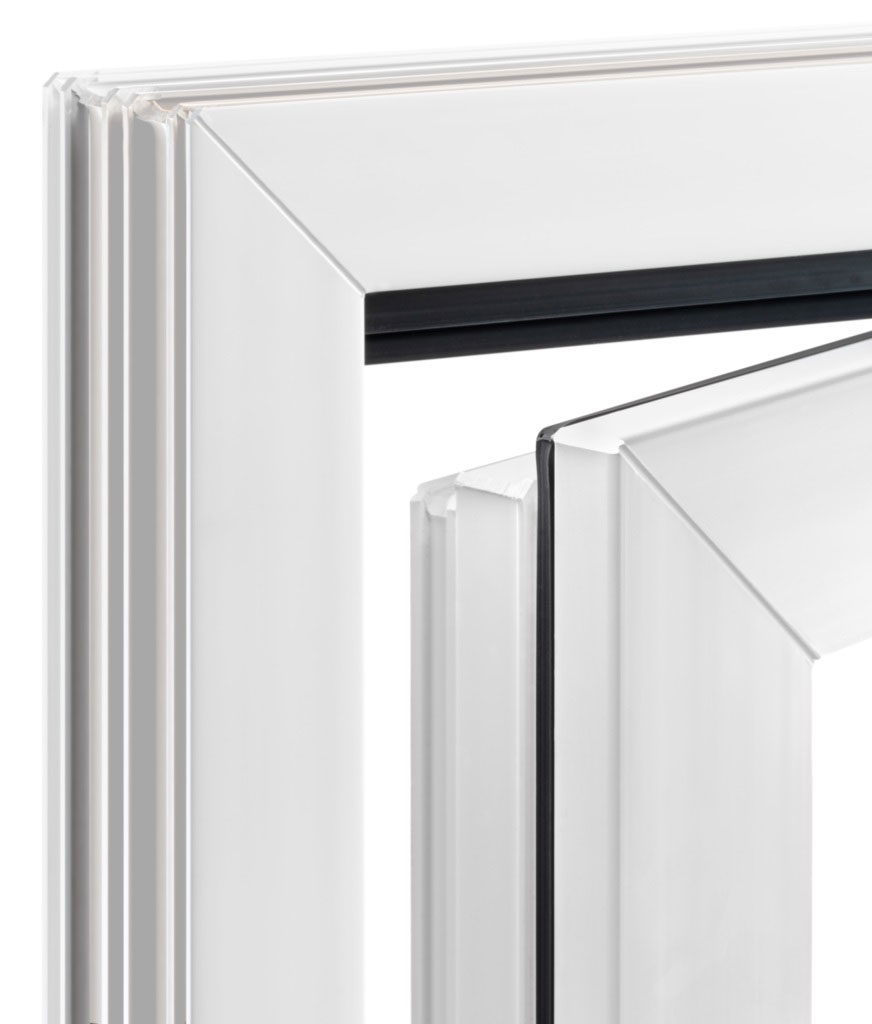
The welding process of Graf Synergy SL4-FF EVO robots is presented in the video:
Traditional welding with a modern twist
The welding process in MS beyond WINDOWS is carried out not only with the use of Graf Synergy SL4-FF EVO robots. The machine park was supplemented with two modern welding and cleaning lines – TURBO T-DRIVE and TURBO S-LINE. It is worth emphasizing that MS more than WINDOW is the first company to have a Stürtz machine in the T-DRIVE configuration. Both lines carry out the process of joining profiles in traditional technology, i.e. with flash. Importantly, the OpticTwinStar and 4MX blast machines are equipped with special “V” knives, which, instead of the standard wide cut on the market, leave a delicate groove with rounded edges. The TURBO T-DRIVE line is presented in the photos below.
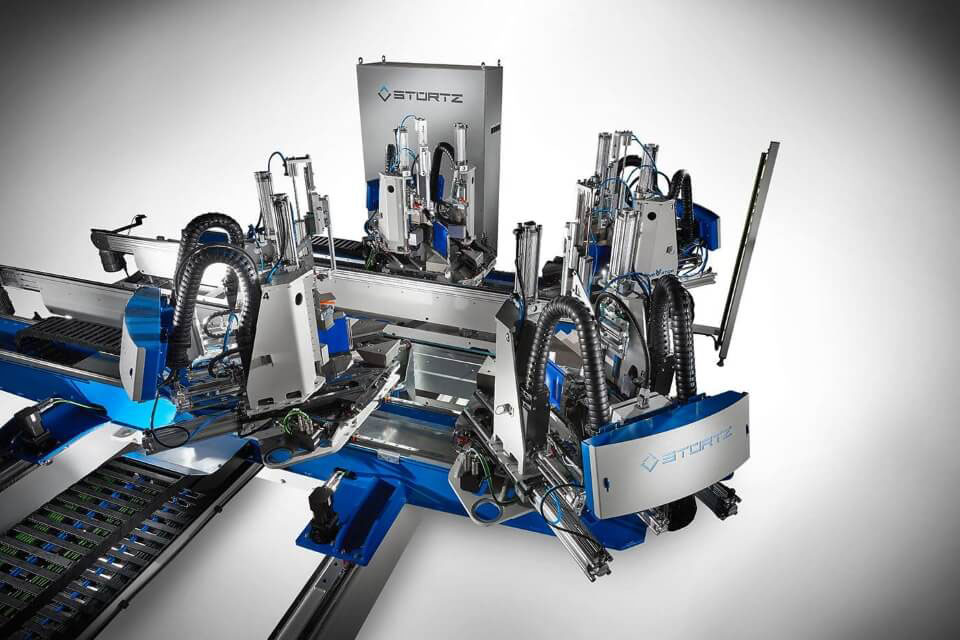
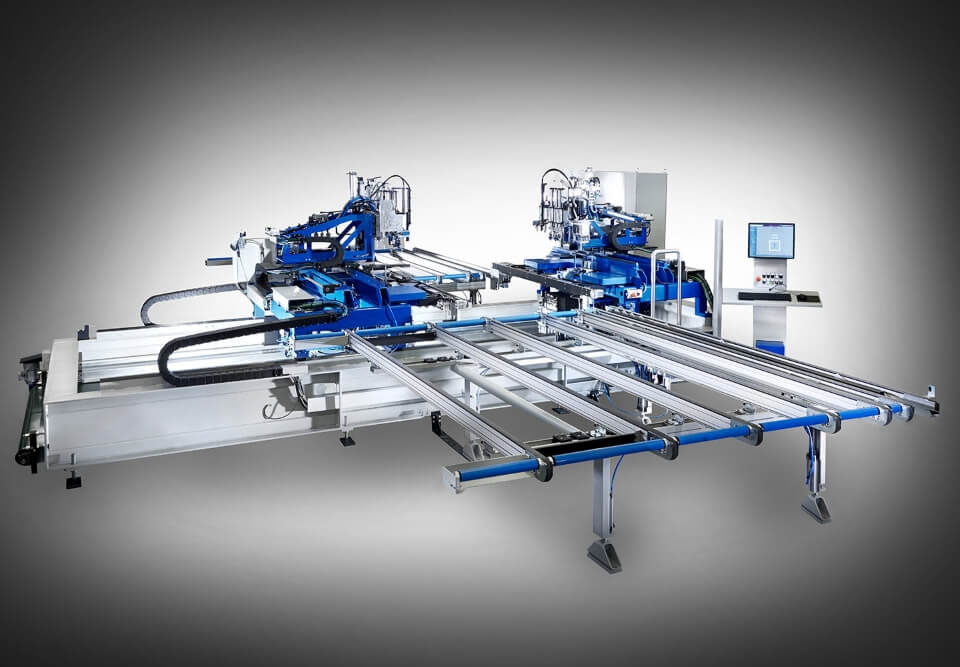